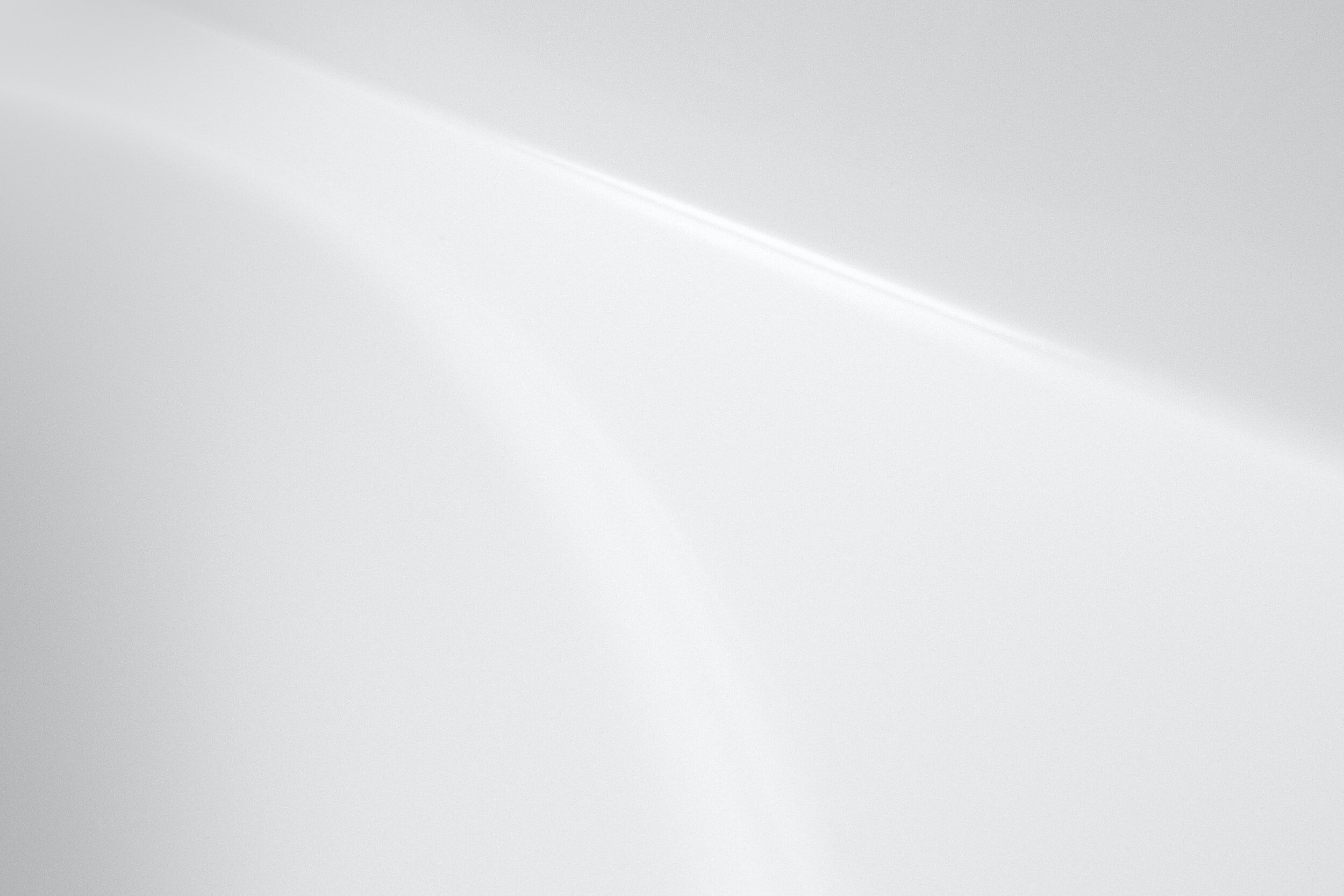
Robotic cells
Deburring
Wet applications with Coolant
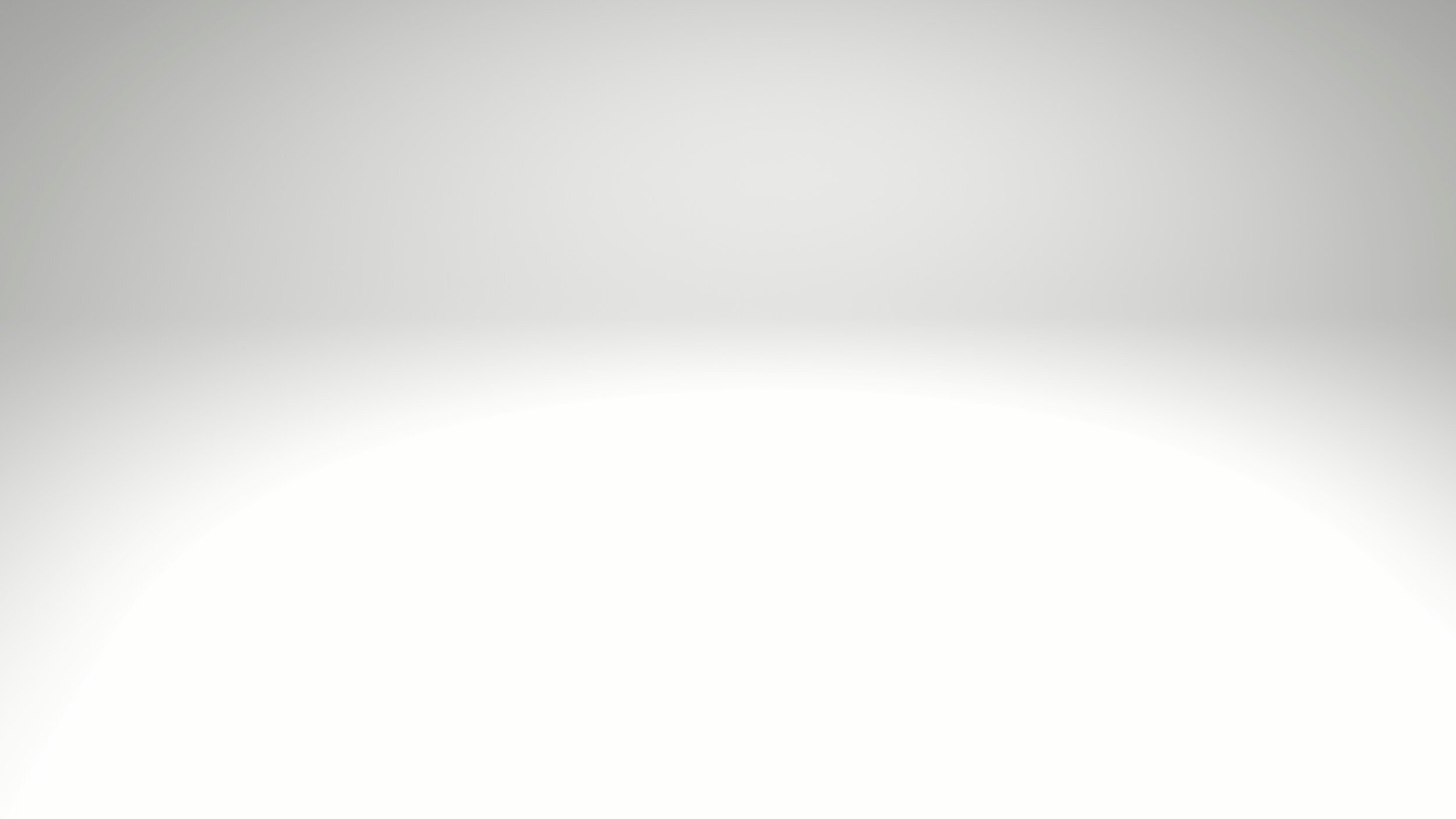
14273
Wet Deburring Cell (multiple holders)
ACT-14273 is a deburring cell for finishing processes requiring liquid coolant and high production rates by handling multiple parts at once. The cell was originally built for deburring of fuel injection holder tubes but can be used in other applications. All components are mounted on compact base with coolant collection and re-circulating system integrated in it. Parts loaded in trays are moved into the cell and located on conveyor. SCARA type robot picks up multiple parts from tray (6 in this case) and brings them to multi-head spindle station where abrasive media deburs all parts in one cycle (in this case bottle brushes). Coolant is automatically sprayed as programmed. Finished parts are placed back in tray and next batch picked up. Once the tray is completed it is conveyed out of the cell and the next one is metered in.
SCARA type robotic arm with multi-gripper end effector
Tray conveyor with metering and locating devices
Multi-head electric motor driven reversible abrasive media spindle
Coolant system
Base and enclosure
Human Machine Interface
Mist collector
Options
Custom part trays
Custom part grippers
For more information, contact us at sales@actrobots.com
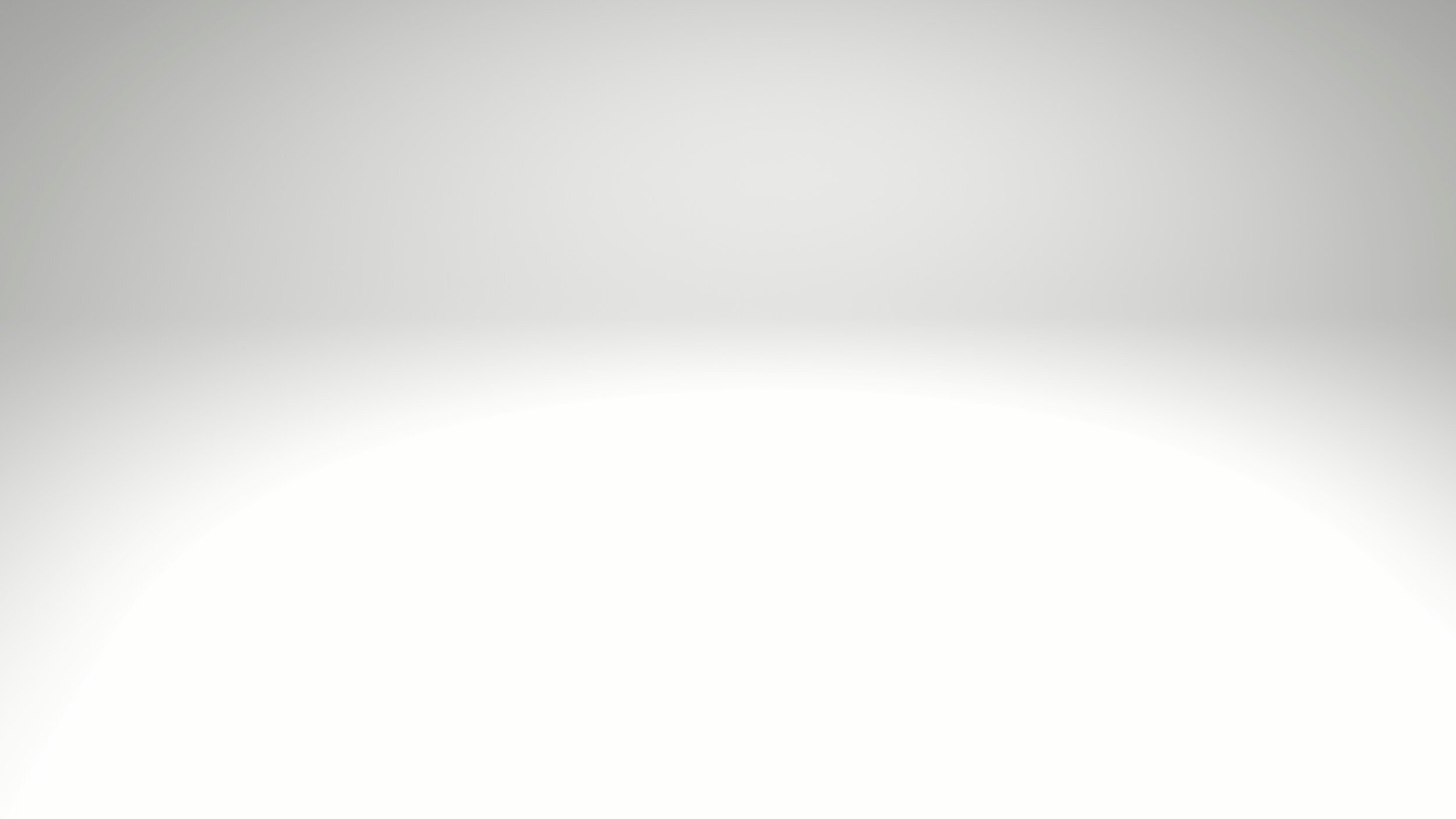
12261
Wet Deburring Cell
ACT-12261 is a deburring cell for processes requiring liquid coolant and high production rates by handling multiple parts at once. The cell was originally used for deburring of fuel injection needles but can easily be adapted for use in other application. All components are mounted on compact base with integrated coolant collection and re-circulating system. Parts located in trays are moved into the cell and located on 2-level conveyor system where the upper level inputs and lower level outputs the trays. The trays are automatically lowered from upper level by an elevator mechanism. SCARA type robot picks up parts from load area (2 at once in this case) and loads them into gripper spindle station on 90 degree indexer at the same time 2 other spindle stations on the indexer perform brushing operations by lowering parts and spinning them in both directions while brushes are moved against them. Last station on indexer has finished parts unloaded from it by another SCARA robot and placed in tray.
Multi-head part spindles on indexer have up/down linear motion and continuous rotation in both directions. Multi-head brush station outside the indexer have linear in/out motion and reversible rotation with speed control. Brush wheel wear is compensated automatically via system software. Coolant is sprayed through multiple nozzles at the brush stations as programmed. Indexer rotates 90 degrees advancing parts from load, through 2 brushing operations, to unload when all station cycles are completed. These rotary process steps allow very high production rates.
SCARA load robot w/ 2 grippers
SCARA unload robot w/ 2 grippers
Part tray 2-level conveyor system with metering and locating mechanisms
Part magazines or trays load area
Two 4-wheel spindle stations
Indexer with 4 multi-head part spindles
4 part spindles with up/down linear motion and reversible speed control rotation of individual part holding heads
Coolant system
Base and enclosure
HMI interface
Mist collector
Options
Custom part trays
Custom part loading mechanisms