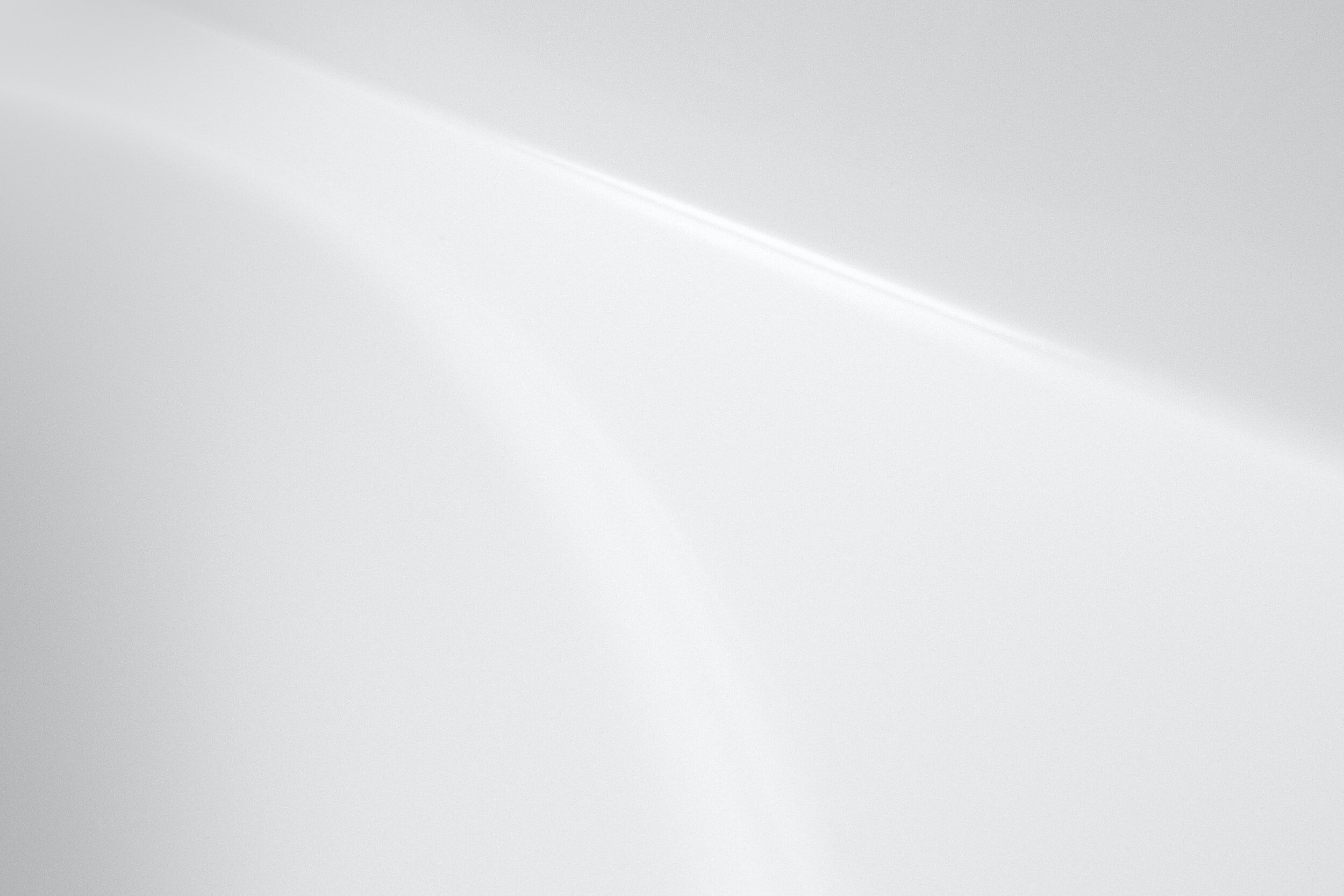
Robotic cells
Grinding / Polishing:
[Media to Part]
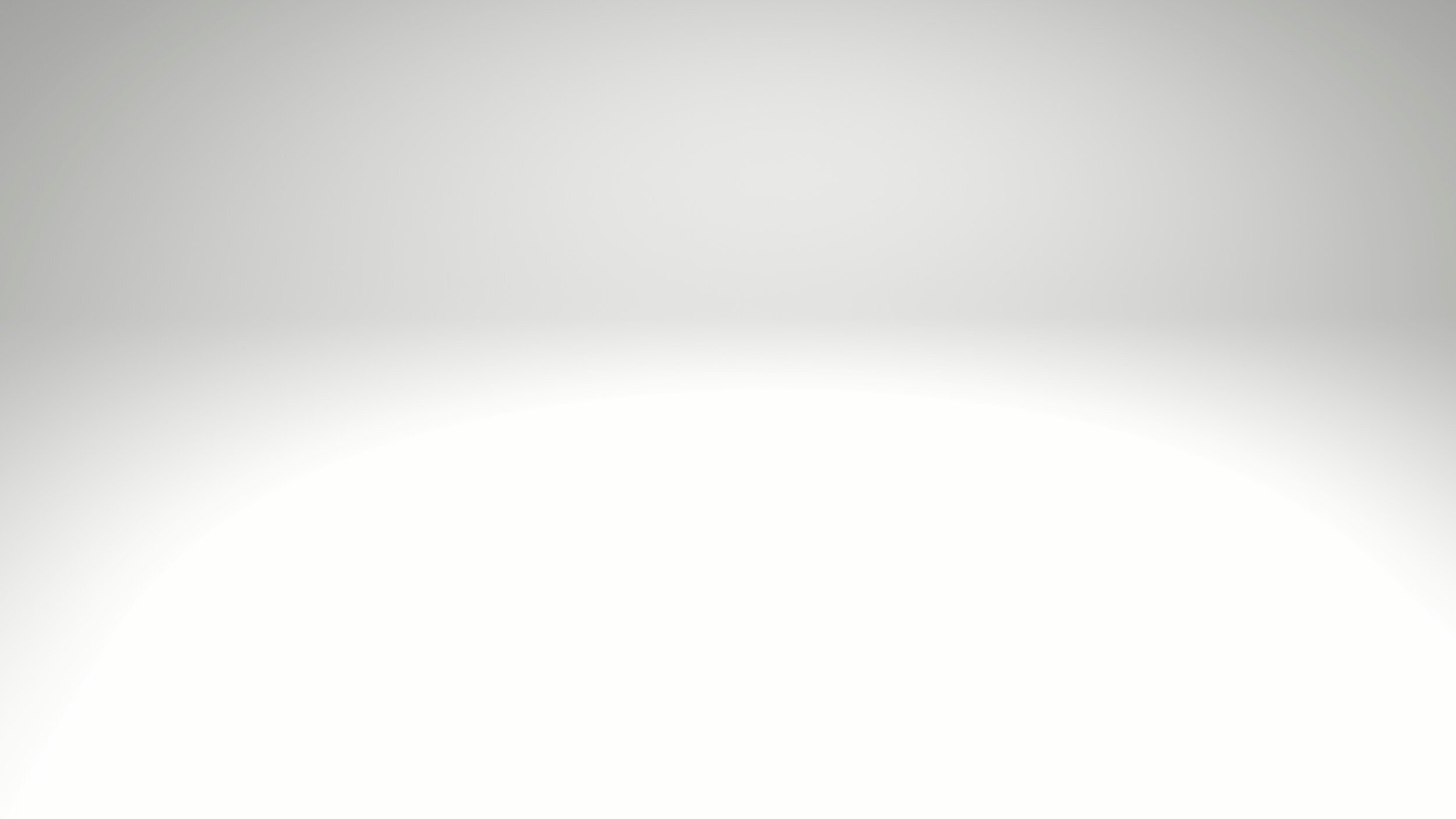
19303
Sink Deflashing and Grinding Cell
ACT-19303 is a robotic grinding or polishing cell originally designed for processing of marble sinks where parts are mounted on fixtures located on 180 deg indexer, rotated inside the cell, and processed with a 90 deg grinder mounted to robotic arm. Dust is collected using wall style collector with circulating air.
Robotic arm (50-80 kg payload)
Grinder, 90 deg, 3HP equivalent, with compliance mounted to robot EOA
Indexer, 180 deg, with part fixtures equipped with pneumatic part clamps
Dust collection system with circulating air
For more information, contact us at sales@actrobots.com
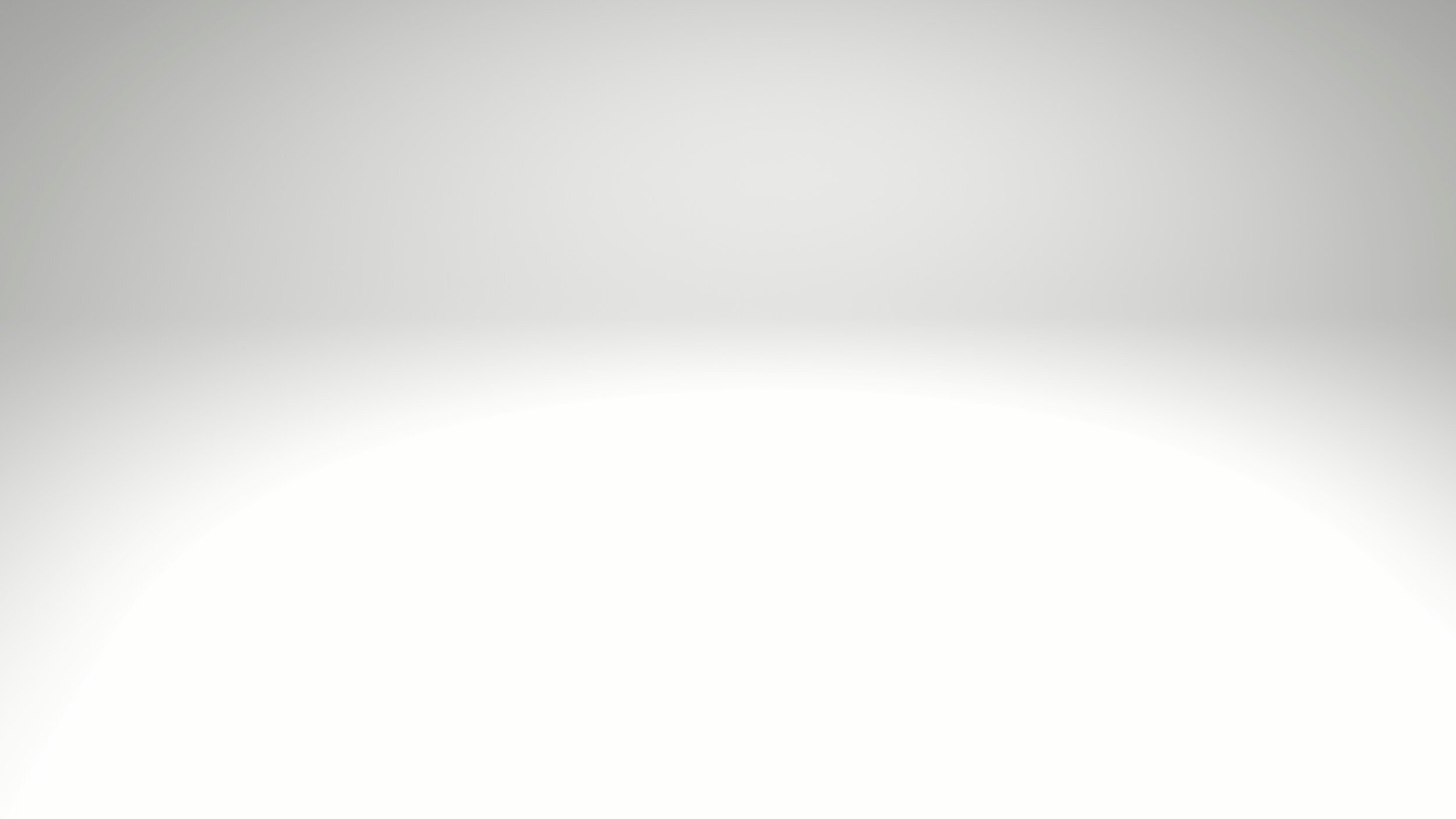
17288
Dual Robotic Cell for Coating Burnishing/Polishing
ACT-17288 is a dual robotic cell for polishing or burnishing Teflon or other coatings on light parts. The process includes measuring incoming parts coating thickness in pre-determined zones using eddy current probes, calculating required process parameters to polish coating to target thickness for each zone, and processing parts based on these calculated parameters. Finished parts were re-measured and before/after data stored in database.
Loading Robot Cell:
Robotic arm (10 kg) with vacuum gripper
Dual eddy current probe tool
Part load and unload drawers
Overhead vision system
Barcode printer
Vision or barcode reader
Polishing Robot Cell:
Robotic arm (20 kg) with servo driven spindle with auto collet
Abrasive disks magazines (hook & loop style)
Disk pads mounted on arbors docked in nests
Automatic abrasive disk application
Disk peeler
Indexer
I/O data network, pneumatics, and power fed to top plate through rotary unions and slip rings for continuous rotation
Vacuum part holding fixtures
Interlocked with both loading and polishing robots
Cell
Enclosure and base
Dust collector
For more information, contact us at sales@actrobots.com
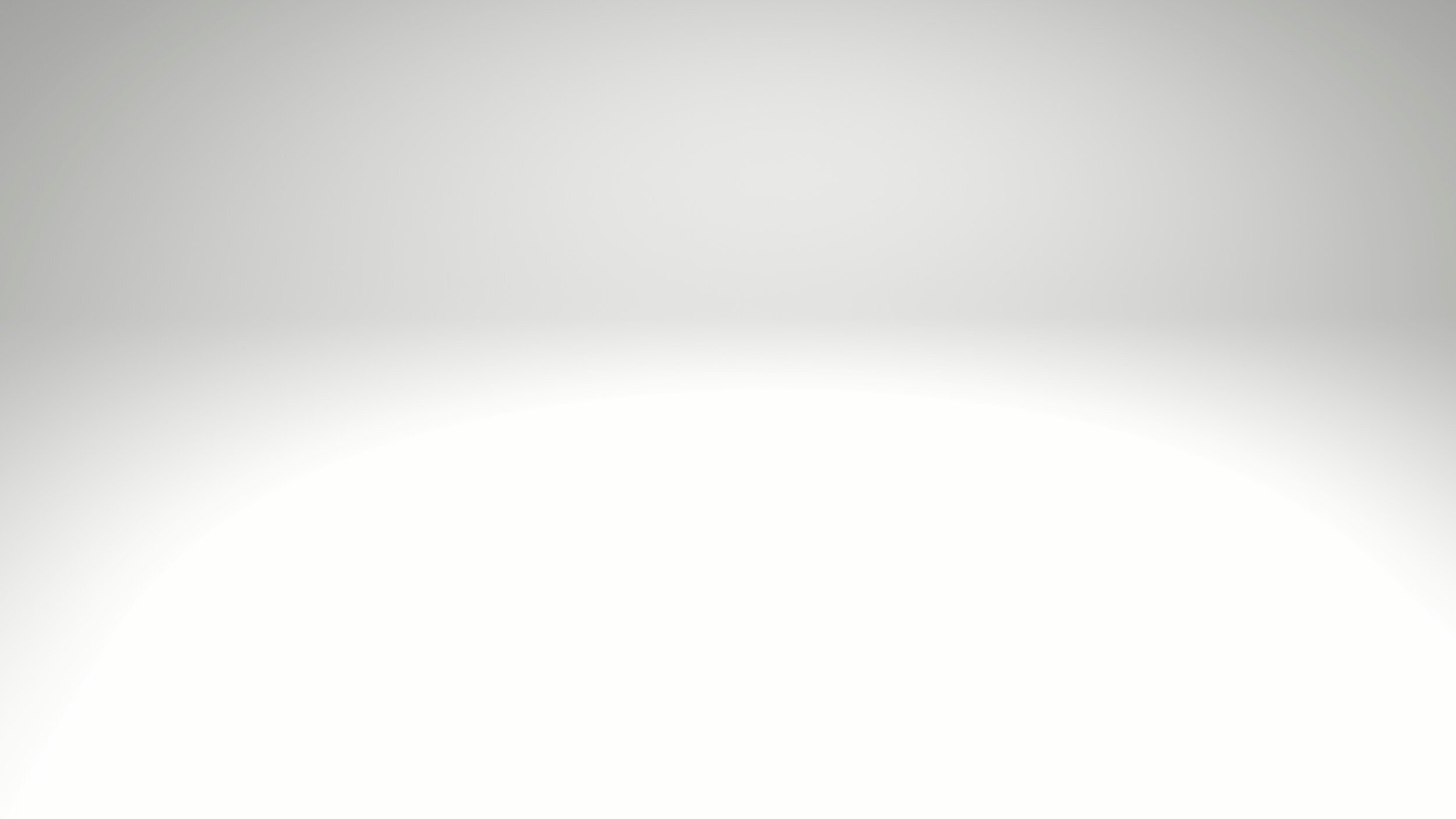
15282
IBR Polishing Cell
ACT-15282 is a robotic cell for automatic polishing of machining lines on IBR blade sides, fillet radius, and air flow path. The cell utilizes robotic arm and series of abrasive belt tools and rotary spindle programmed to gradually polish all IBR blades in pre-determined sequence. As belts and other abrasive are used the robot swaps tools with fresh abrasives to continue its polishing operations on the rest of IBR blades.
Parts are loaded on servo controlled rotary table, automatically positioned by locating first blade before the polishing process begins. Offline motion programming software allows development of complex tool paths on contoured surfaces such as concave ad convex blade sides. Latest in robotic safety devices and methodologies compliant with RIA regulations are used. The entire system is surrounded by a dust and sound reducing enclosure with door safety interlocks.
Robot arm payloads: 50kg
Automatic tool changer
Servo controlled rotary table with part chuck
Tool magazine with belt and spindle tools
ACTView Human Machine Interface software
Common base and full enclosure
For more information, contact us at sales@actrobots.com
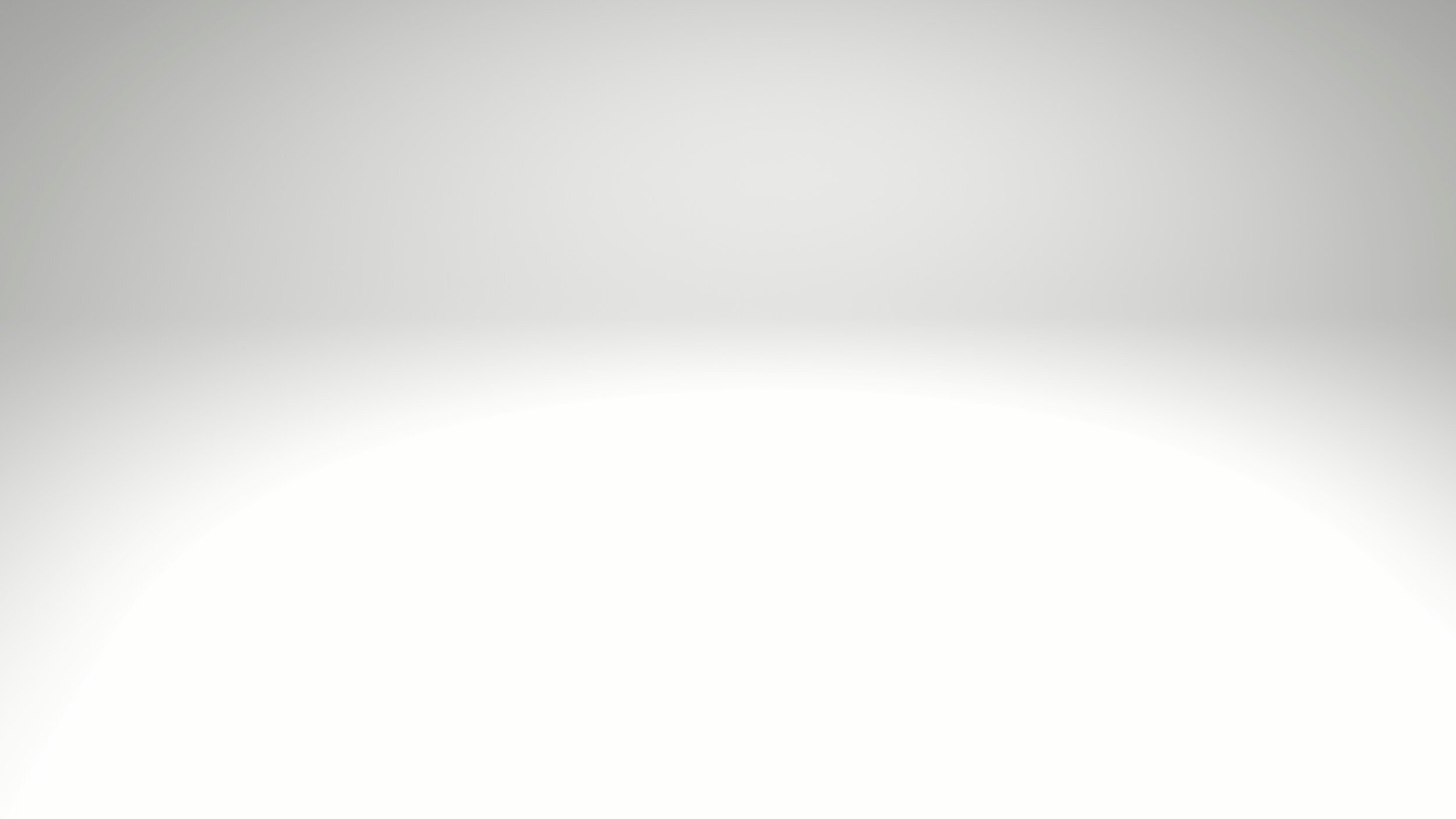
11257
Polishing and Buffing of Kettles
ACT-11257 is a drum shaped parts polishing and buffing cell (kettles). Parts are loaded onto the rotary spinner table and upon starting program execution, the robot arm performs part fixture adjustments for the part type and size. The fixtures were designed to be adjustable for holding down drum rims of parts without bottom fixturing features. Next, robot equipped with 5-10HP servo drive spindle with auto collet would pickup series of programmed abrasives mounted on 1" diameter arbors and docked in nests in tool magazine. The abrasives were used for polishing drum surfaces while part was spinning. Some finishing steps were buffs with compound which was applied automatically in the dual compound station. Vacuum tool is included for automatic vacuuming of polishing dust from part surfaces.
Robotic arm (80-150 kg payload)
Auto collet servo driven spindle (10-13HP)
Tool magazine with various arbors and abrasives
Dual compound application station
Part rotary spinner
Part hold-down fixtures with automatic size adjustments
Options
Industrial vacuum tool system
Human Machine Interface