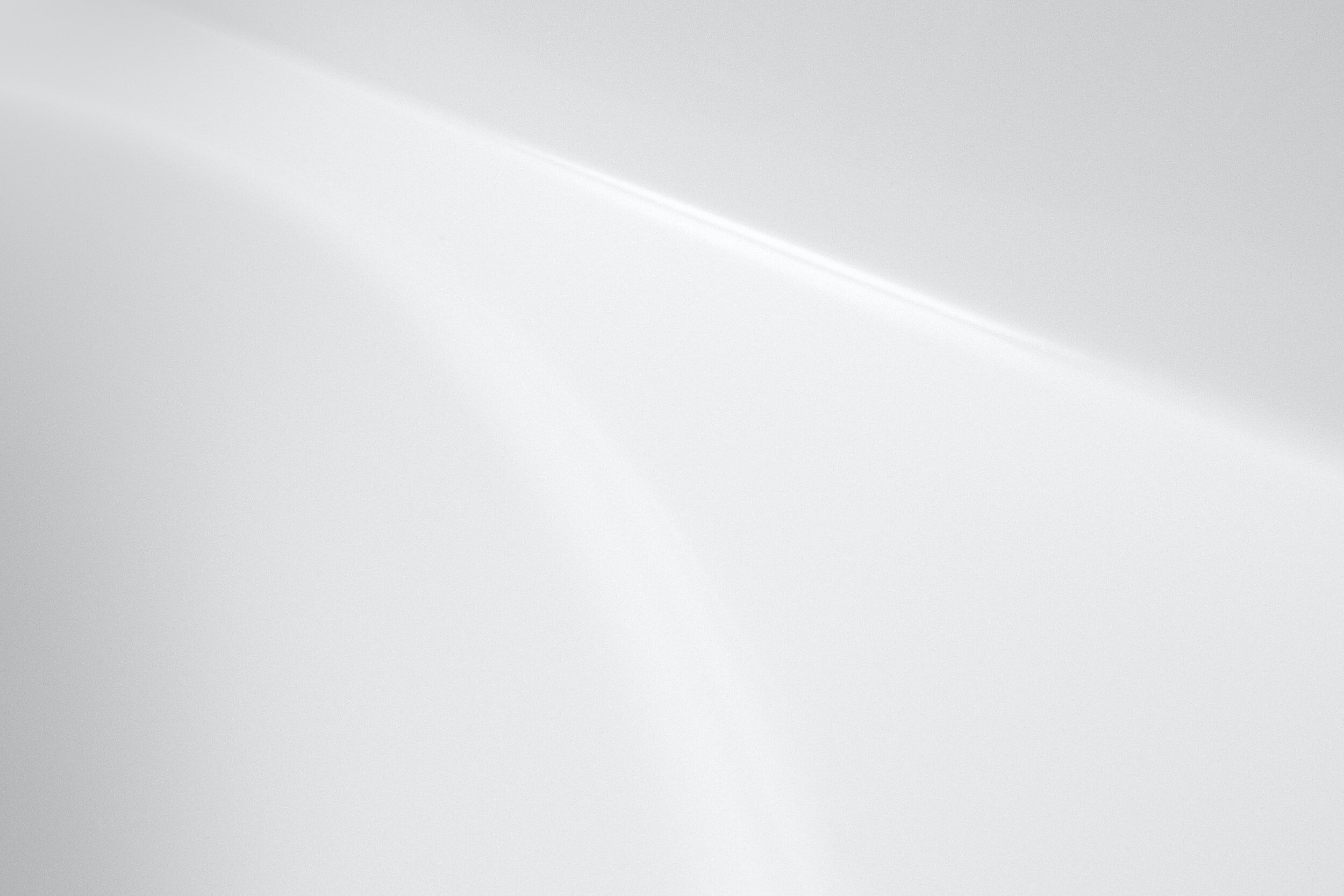
Robotic cells
Grinding / Polishing
Part to Media
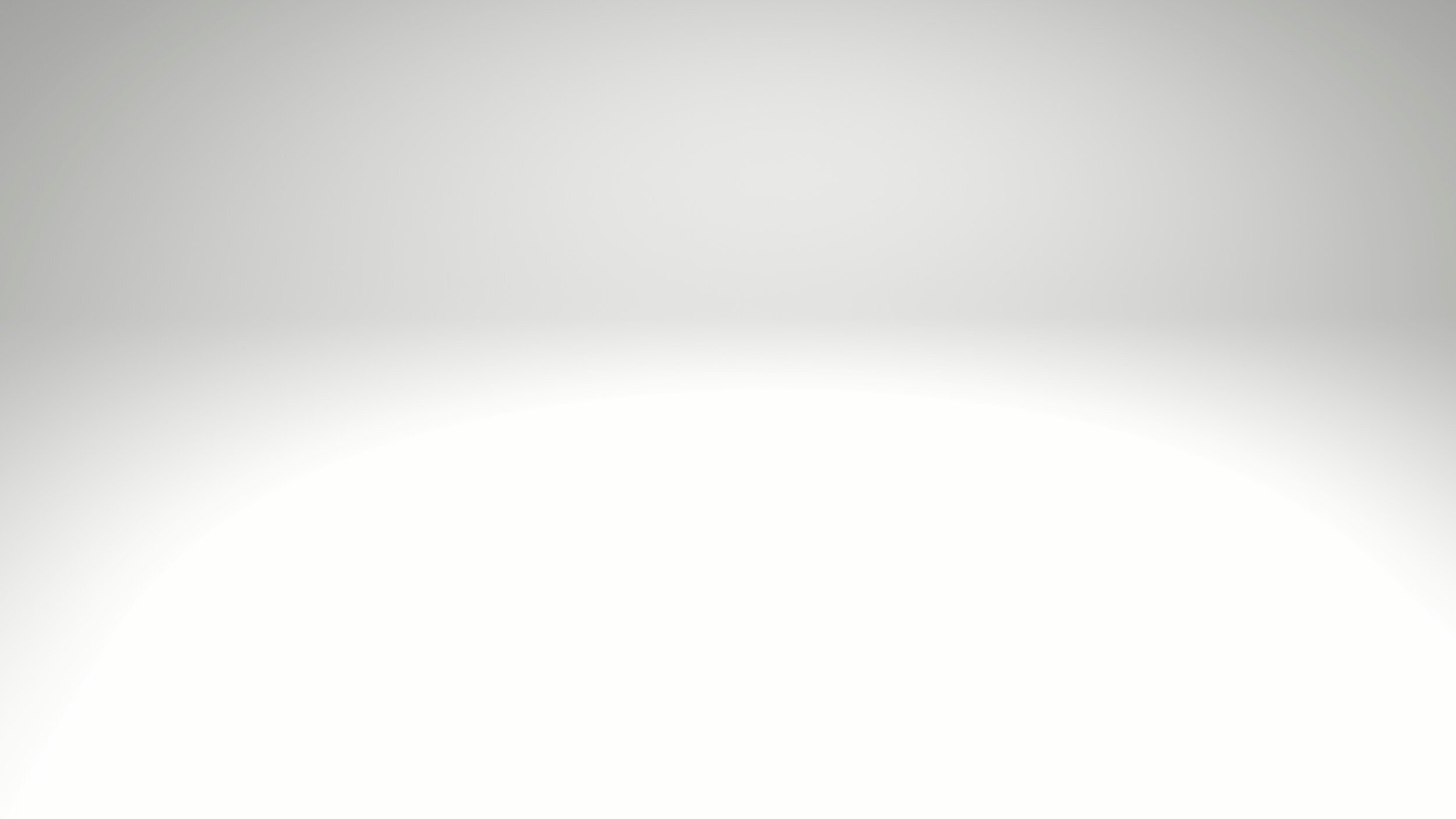
15284
Dual cell with Center Part Feed Conveyor
ACT-15284 is a robotic grinding/polishing system made up of 2 robotic cells and a part feed conveyor. The conveyor detects parts fed in standard plastic trays and automatically distributes them to robotic cells for processing. Then, the parts are picked up from simple tray nests using vision and processed on the belt, 2 abrasive wheels, and/or drill/reamer stations. Finished parts are dropped on the exit chute to be collected in customer bins. The robots automatically pick the tool/gripper from the magazine based on the incoming part number.
Robot arm with 50-80 kg payload (Yaskawa or ABB)
Automatic tool changer EOAT
Robot mounted vision system
5 HP belt grinding head
5 HP dual wheel head with wheel wear sensors
Tool/Gripper magazine with 3 or 6 docking nests
3 or 6 Gripper assemblies
Part exit chute
Enclosure and Base
Dust collection ducting with automatic gates
Human Machine Interface (HMI)
For more information, contact us at sales@actrobots.com
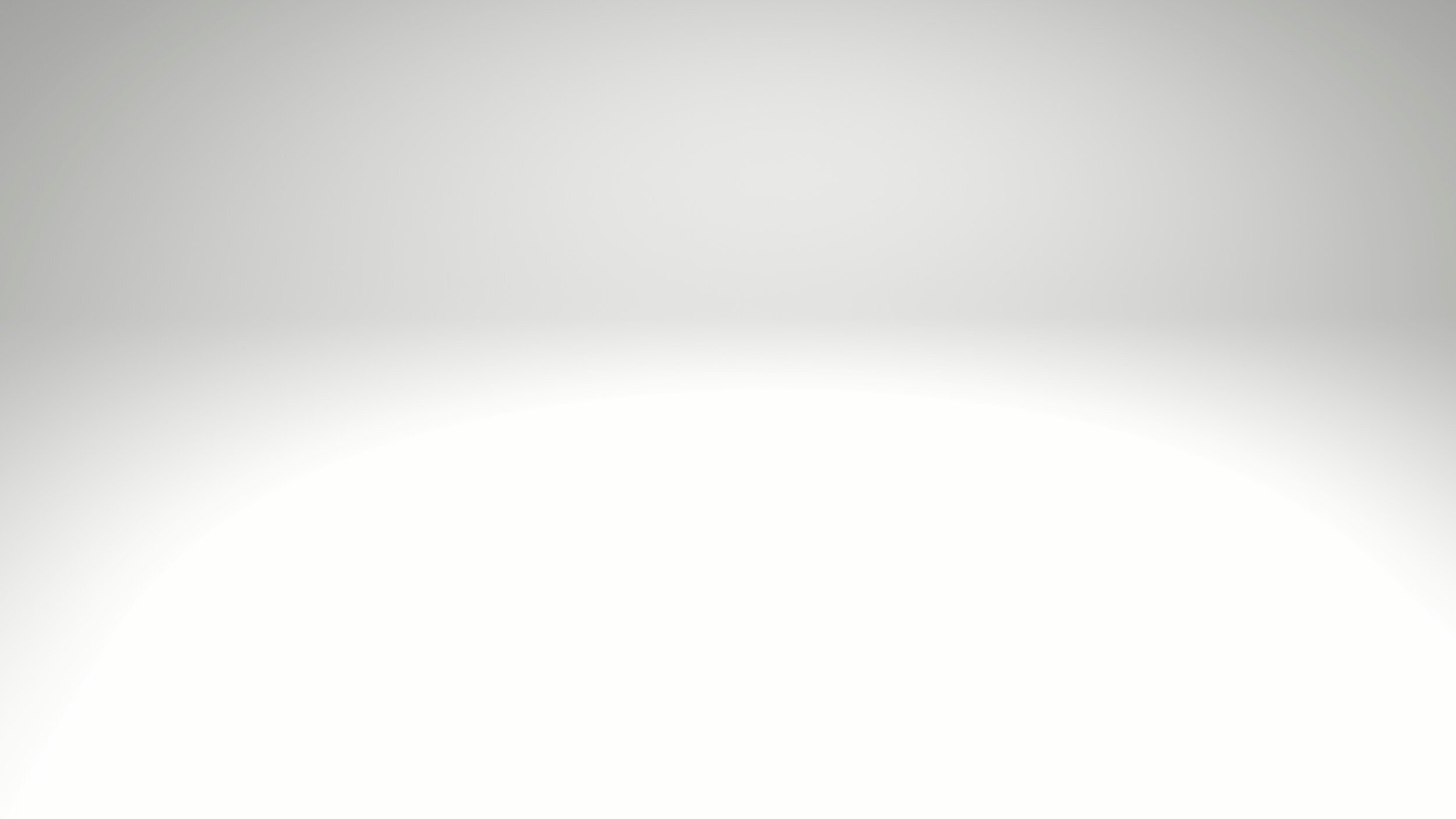
17292
Single Cell with Part Feed Conveyor
ACT-15284 is a robotic grinding/polishing system made up of 2 robotic cells and a part feed conveyor. The conveyor detects parts fed in standard plastic trays and automatically distributes them to robotic cells for processing. Then, the parts are picked up from simple tray nests using vision and processed on the belt, 2 abrasive wheels, and/or drill/reamer stations. Finished parts are dropped on the exit chute to be collected in customer bins. The robots automatically pick the tool/gripper from the magazine based on the incoming part number.
Robot Arm with 50-80 kg payload (Yaskawa or ABB)
Automatic tool changer EOAT
Robot mounted vision system
5 HP Belt grinding head
5 HP Dual wheel head with wheel wear sensors
Tool/Gripper magazine with 3 or 6 docking nests
3 or 6 gripper assemblies
Part exit chute
Enclosure and Base
Dust collection ducting with automatic gates
Human Machine Interface (HMI)
For more information, contact us at sales@actrobots.com
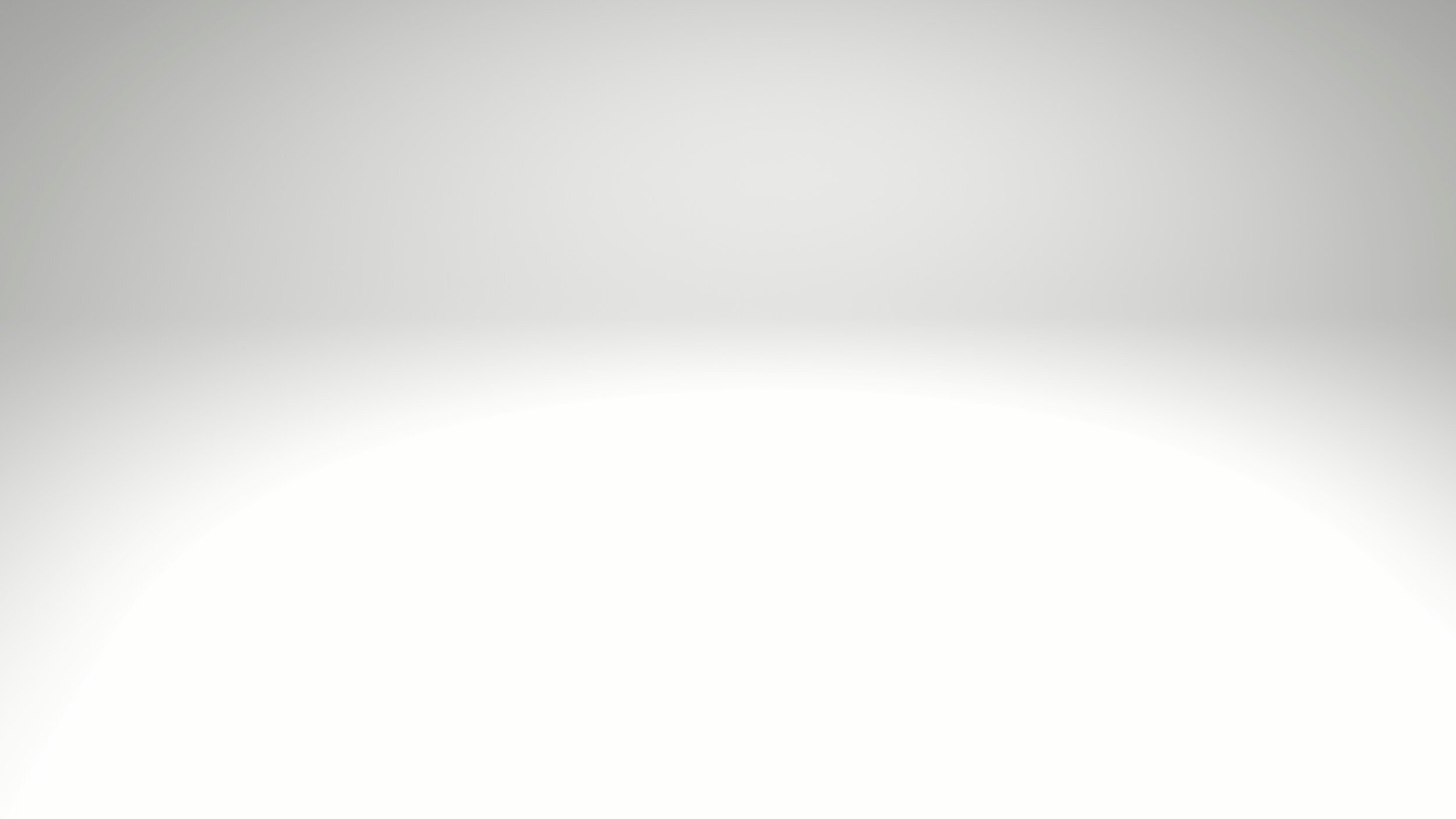
17287
Single Cell with Part Feed Conveyor
ACT-17287 is a grinding/polishing system. The conveyor detects large fed parts and automatically distributes them for processing. Then, the cell parts are picked up from the conveyor and processed on the belt, 2 abrasive wheels, and/or drill/reamer stations. Finished parts are placed back on the conveyor. The robots automatically pick the tool/gripper from the magazine based on the incoming part number.
Robot arm 120-350 kg payload (Yaskawa or ABB)
10 HP belt head with linear compliance
10 HP dual wheel head with linear and automatic wear compensation
Automatic tool changer EOAT
Robot mounted vision
Tool magazine with docking nest for grippers and tool assemblies
90 deg grinder tool, debur tool assembly, 3-4 gripper assemblies
Enclosure and Base
Dust Collection ducting with automatic gates
Human Machine Interface (HMI)
For more information, contact us at sales@actrobots.com
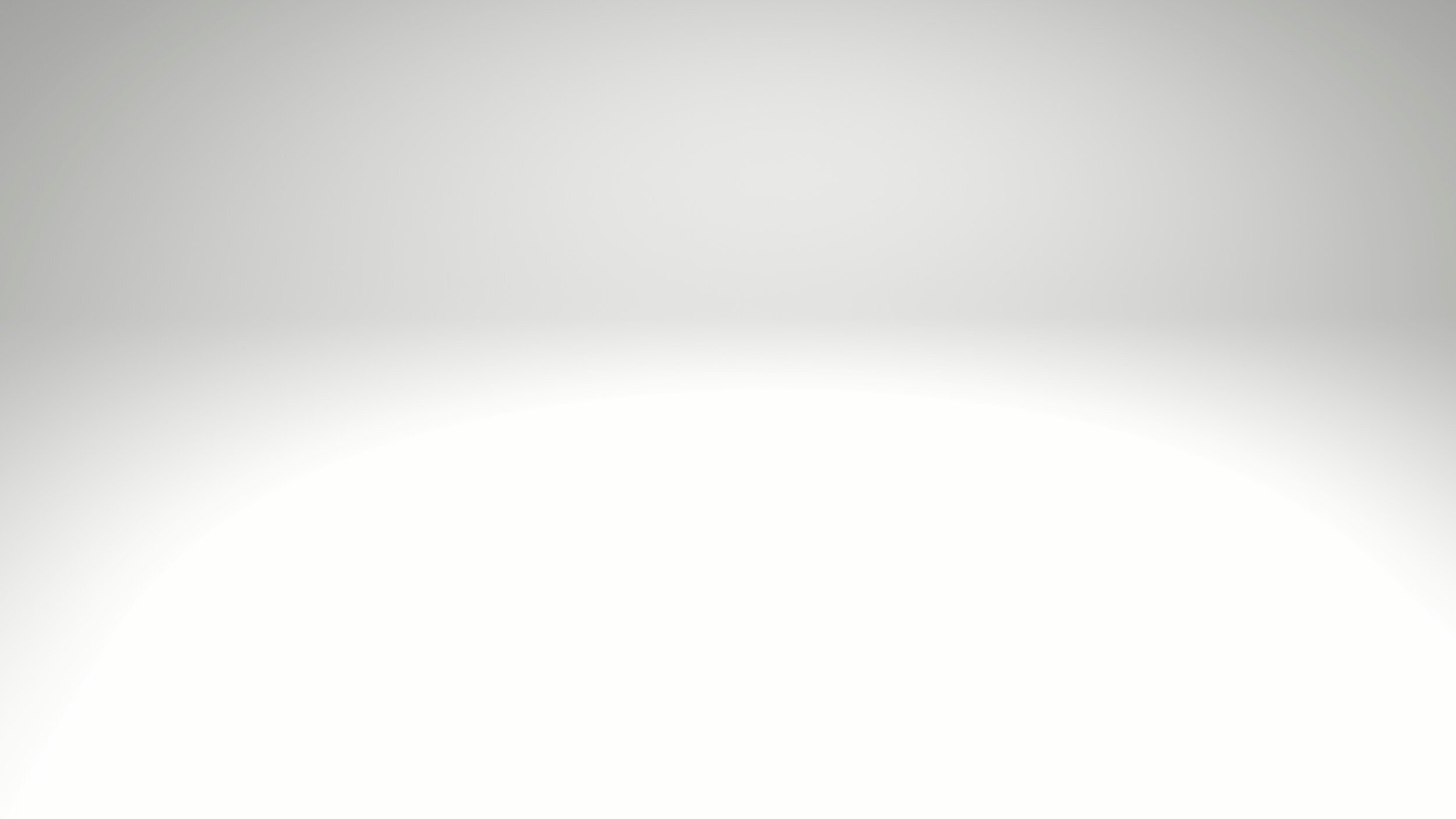
18296
Dual Cells, Robot and Tool Magazine in Between
ACT-18296 is a robotic polishing or grinding system consisting of 3 areas. The center area includes part load drawers, and the robot and tool magazine. The left and right areas are redundant process areas where the robot switches part processing based on the abrasive configuration and part recipe. Polishing or grinding operations can be programmed to be done in one area with an automatic switch to the other when abrasives reach maximum wear. Both can be employed at the same time when a multi-abrasive process is needed.
Two 5 HP belt head with linear compliance
5 HP single wheel head with linear compliance
Overhead safety roller gate
Triple vertical drawer part load magazine
50-80 kg robotic arm
Automatic tool changer end of arm
Tool magazine with up to 20 tool/gripper docking nest
Enclosure and Base
Dust collection ducting with automatic gates
For more information, contact us at sales@actrobots.com
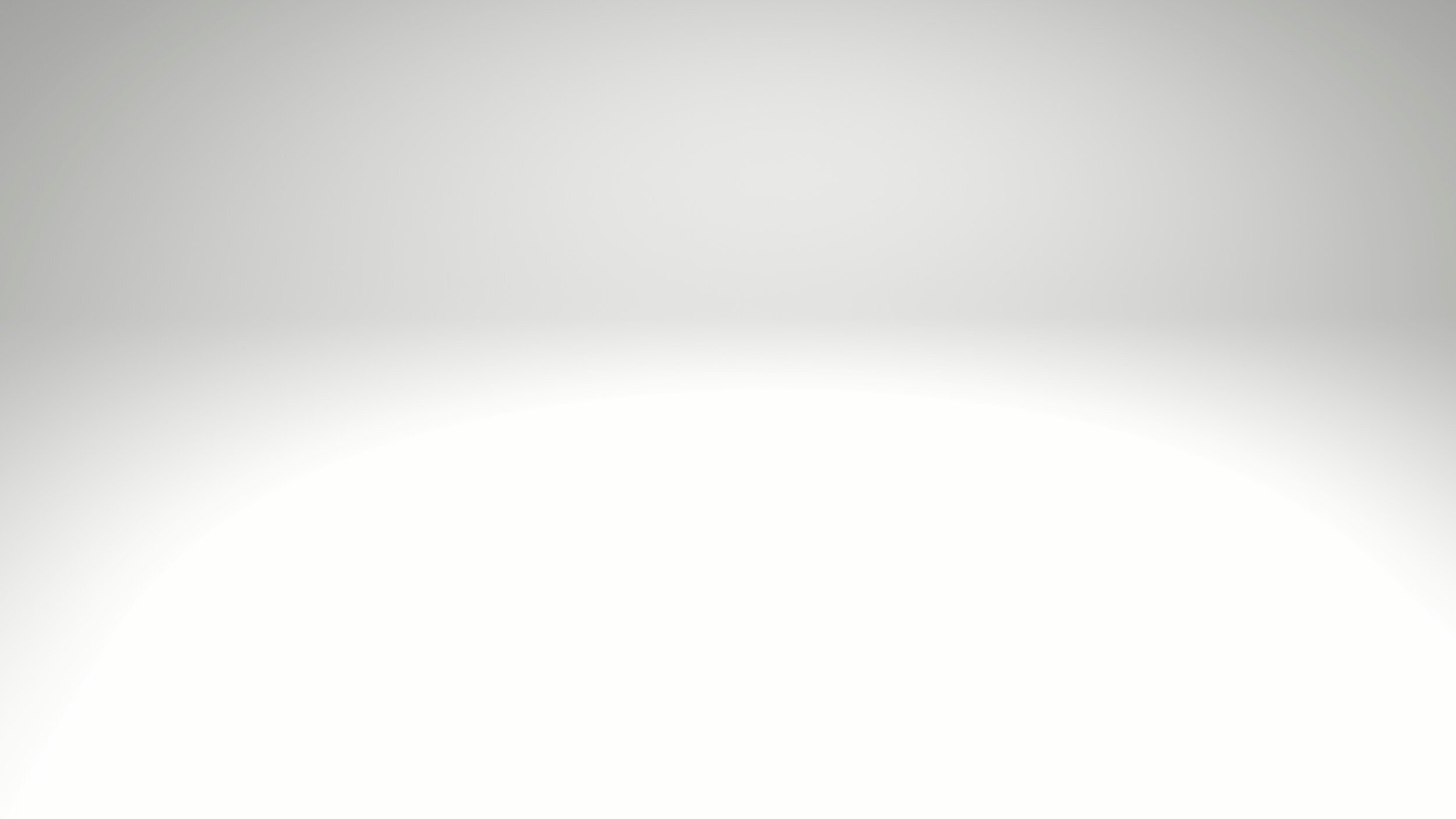
14274
Polishing Cell with 1 Belt & 2 Wheels
ACT-14274 is a polishing cell designed for smaller parts such as bathroom and kitchen faucet fixtures. It consists of a robot arm with a gripper EOA, 5 HP belt head, two 5 HP wheel heads, and a dual drawer part load mechanism.
Robot arm with 20 kg payload
Gripper and pass-through device EOAT
5 HP belt head with linear compliance
Front and reverse belt configuration arm
Two 5 HP single wheel heads with linear compliance
Wheel wear sensor
Dual drawer part load station
Enclosure and Base (7H x 10H x 8H)
Part exit chute
Enclosure and Base
Dust collection ducting with automatic gates
Human Machine Interface (HMI)
For more information, contact us at sales@actrobots.com
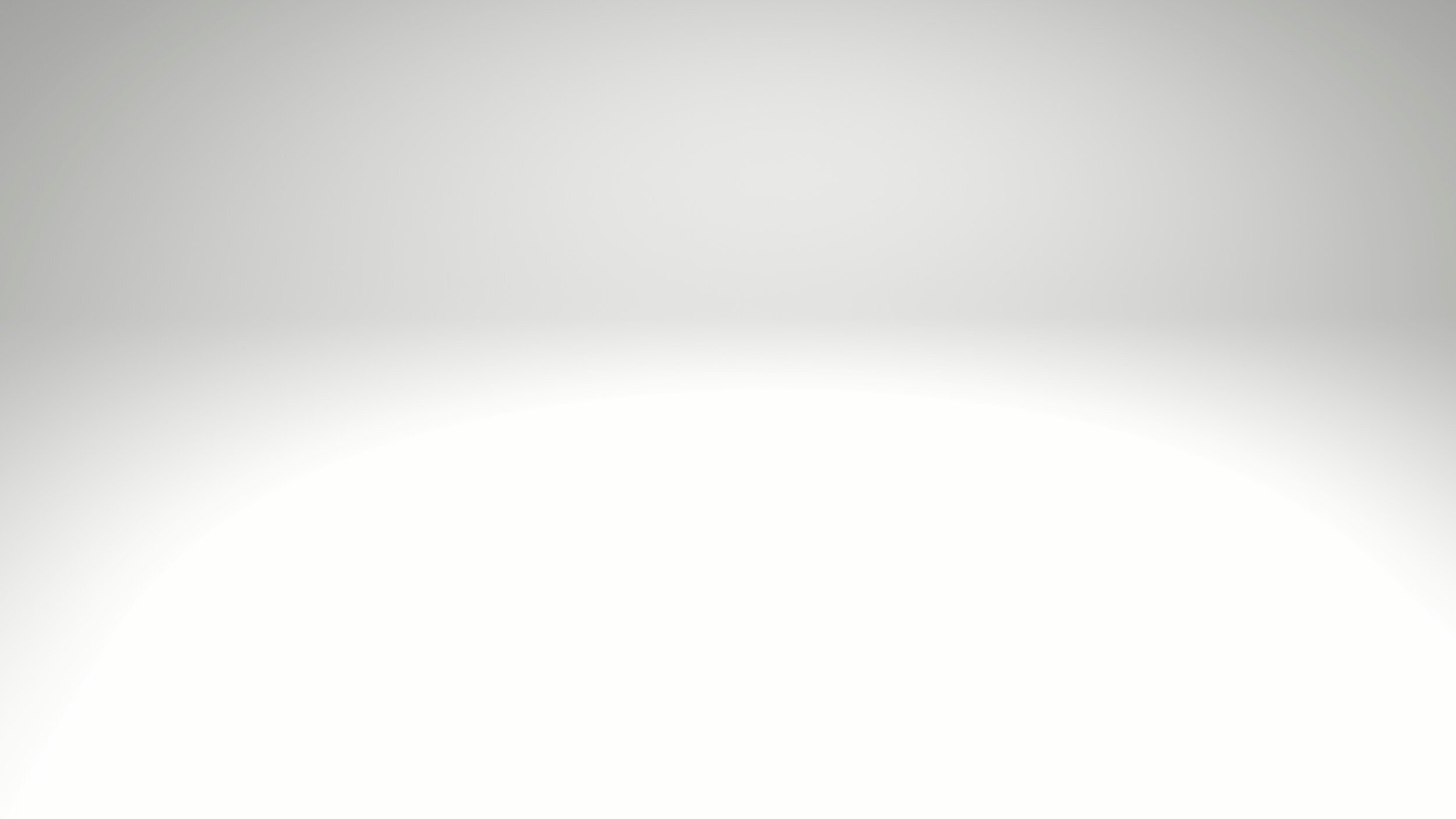
13270
Coating Thickness Polishing
ACT-13270 is a portable robotic polishing or deburring cell originally designated for coating stripping and polishing. The coatings could be plasma spray of aerospace components. The process consists of picking parts from static load nests after vision detection, polishing on 2 servo driven wheel spindles, and dropping them off at the unload area. Polishing includes closed loop force control
Robot arm with 6 kg payload
Automatic tool changer EOA
Tool/gripper magazine
Two servo drive wheel spindles w/ auto collets
Automatic wheel change picture with gripper, arbors, and docking nests
Part load and unload areas w/ vision and safety
Human Machine Interface
Enclosure and base (61" x 61" x 94")
Dust collection ducting
For more information, contact us at sales@actrobots.com
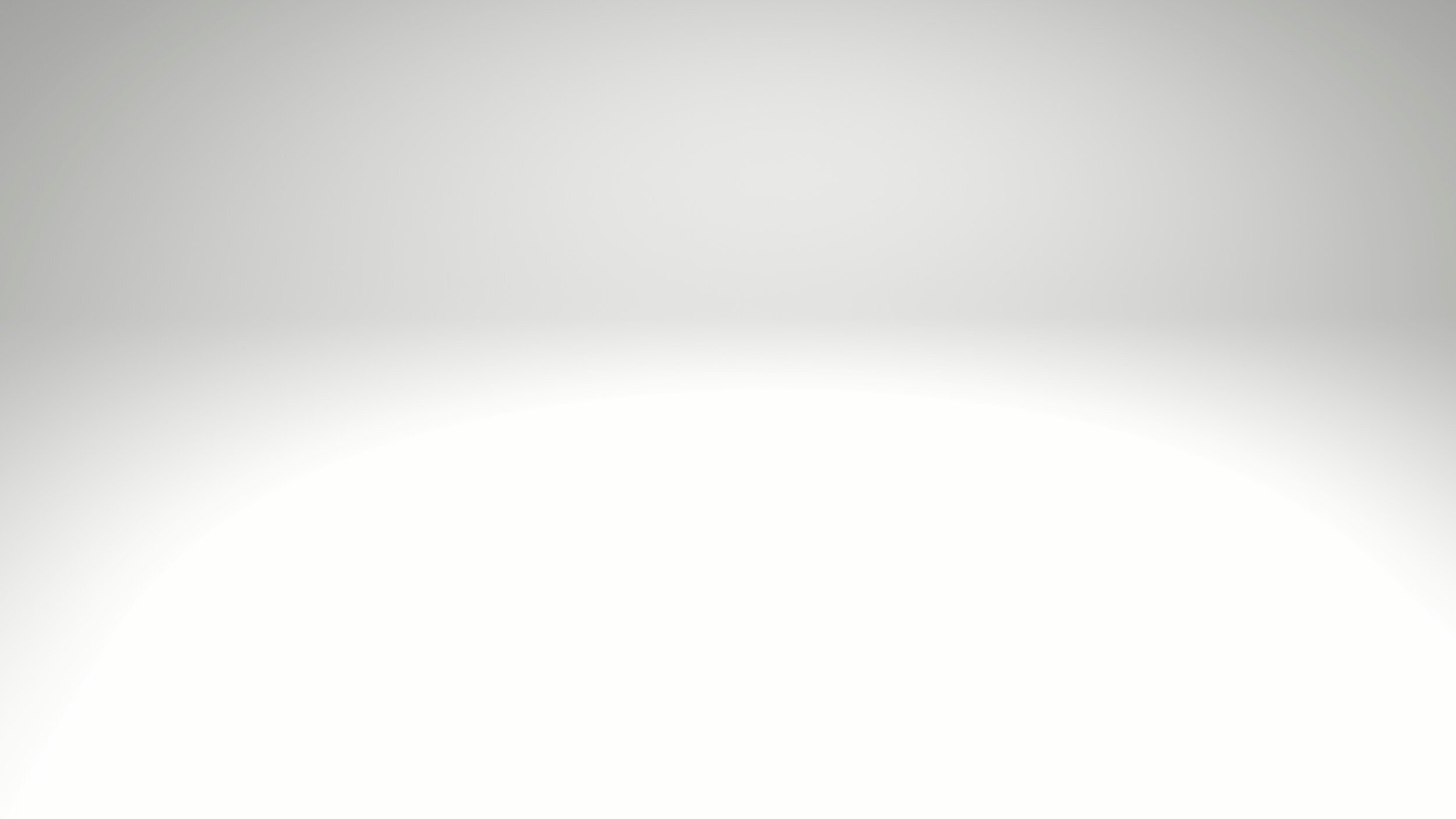
17997-0000
Polishing or Deburring Cell
ACT-17997 is a polishing or deburring robotic cell with a base floor integrated down-draft style dust collector. This cell is portable and self contained with 6-10 kg robotic arm, part load drawer, rotary indexer tool magazine, high speed debur spindle, small wheel spindle, 2HP belt station, 5HP wheel head, small belt head, and dust collector in the floor.
Robot Arm (6-10 kg) w/ auto tool changer EOA
High speed deburring spindle with 360 deg compliance
Servo or air driven spindle for small wheels up to 6" OD
Belt head, 2HP
Wheel head, 5HP, for large abrasive wheels up to 16" OD
Small belt tool with radial compliance for belts up to 1/2" W x 18" L
Part load drawer
Rotary indexer tool magazine with up to 16 tool docking positions
Down-draft dust collector integrated in machine base
Enclosure and base
Human Machine Interface (HMI)
For more information, contact us at sales@actrobots.com
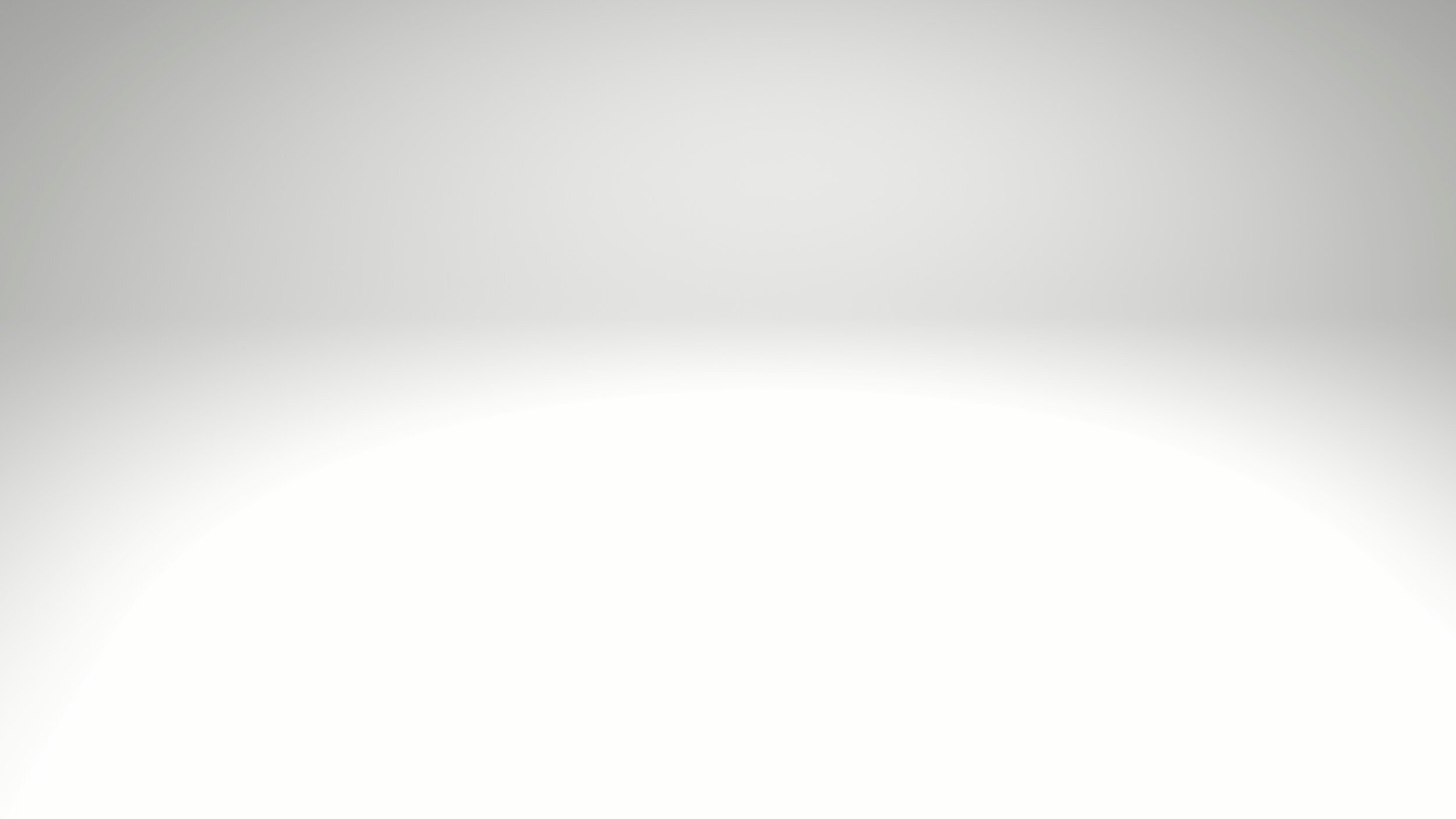
12262
Grinding Cell with 2 Belts
ACT-12262 is a robotic grinding cell for medium size parts such as wrenches and pliers, with a robotic arm part load indexer, two heavy duty 5HP belt heads, and a part exit chute.
Robotic arm (50-80 kg payload) with gripper EOAT
Two heavy duty 5HP belt grinding heads with linear compliance
Indexer with framing for part load fixtures
Dust collection ducting, scoops, and automatic gates
Enclosure and base
Human Machine Interface
Options
Vision or laser scanner to measure part deformation and offset robot motion
Automatic tool change adapters
Tool magazine
For more information, contact us at sales@actrobots.com
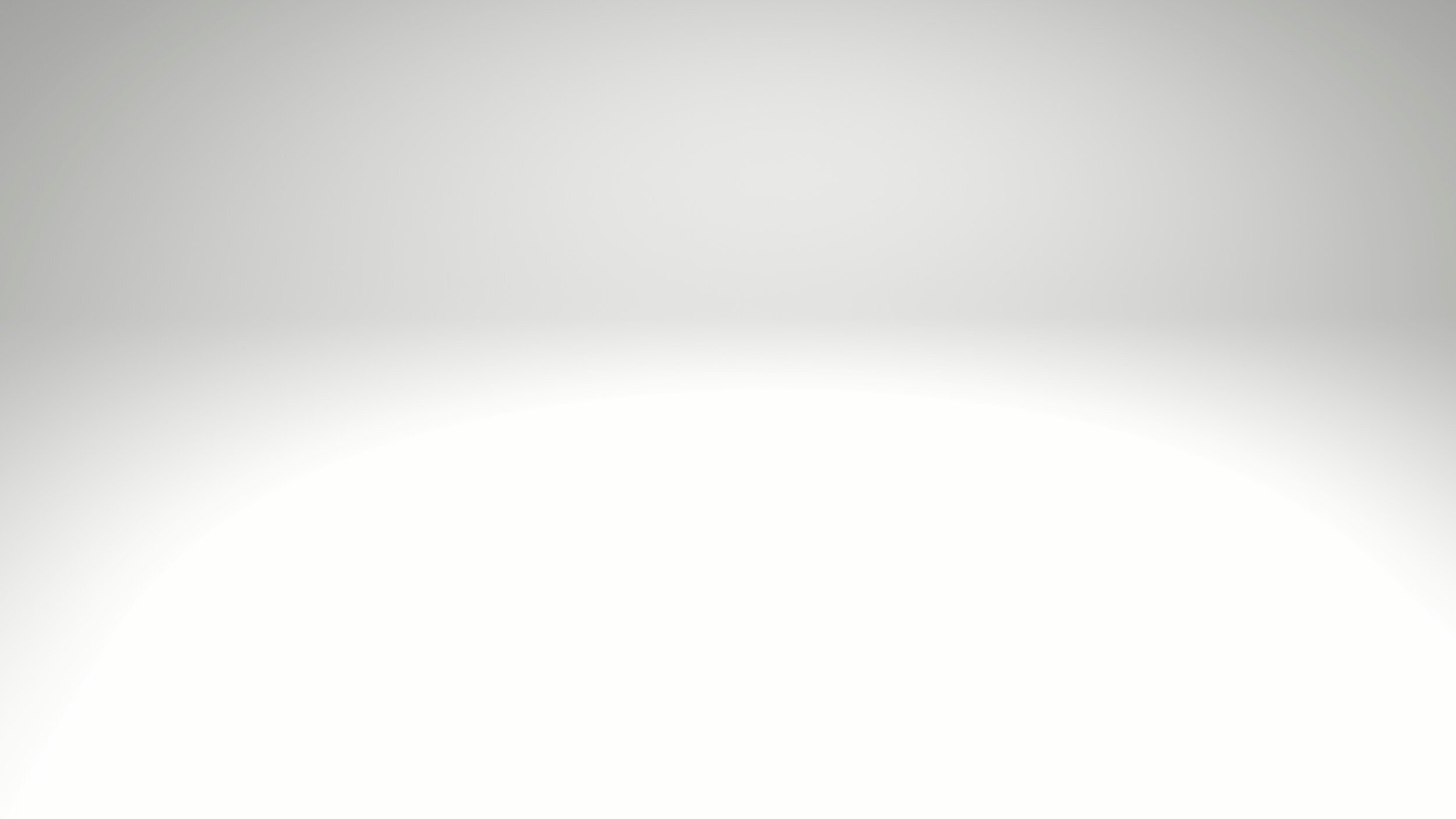
07229
Cell with 3 Belts and Tombstone
ACT-07229 is a polishing or grinding cell for parts such as door handles or faucet fixtures, requiring a 3-5 step abrasive process.
Robotic arm (50-80 kg payload) with gripper EOA
Three 5HP belt heads with linear compliance
Dual wheel 5HP head
4-sided vertical part load magazine (tombstone) on 90 deg indexer
Human Machine Interface
Enclosure and base
Options
Automatic wheel wear measuring sensor
Dust collector
Laser scanner for part measuring and offsets
For more information, contact us at sales@actrobots.com
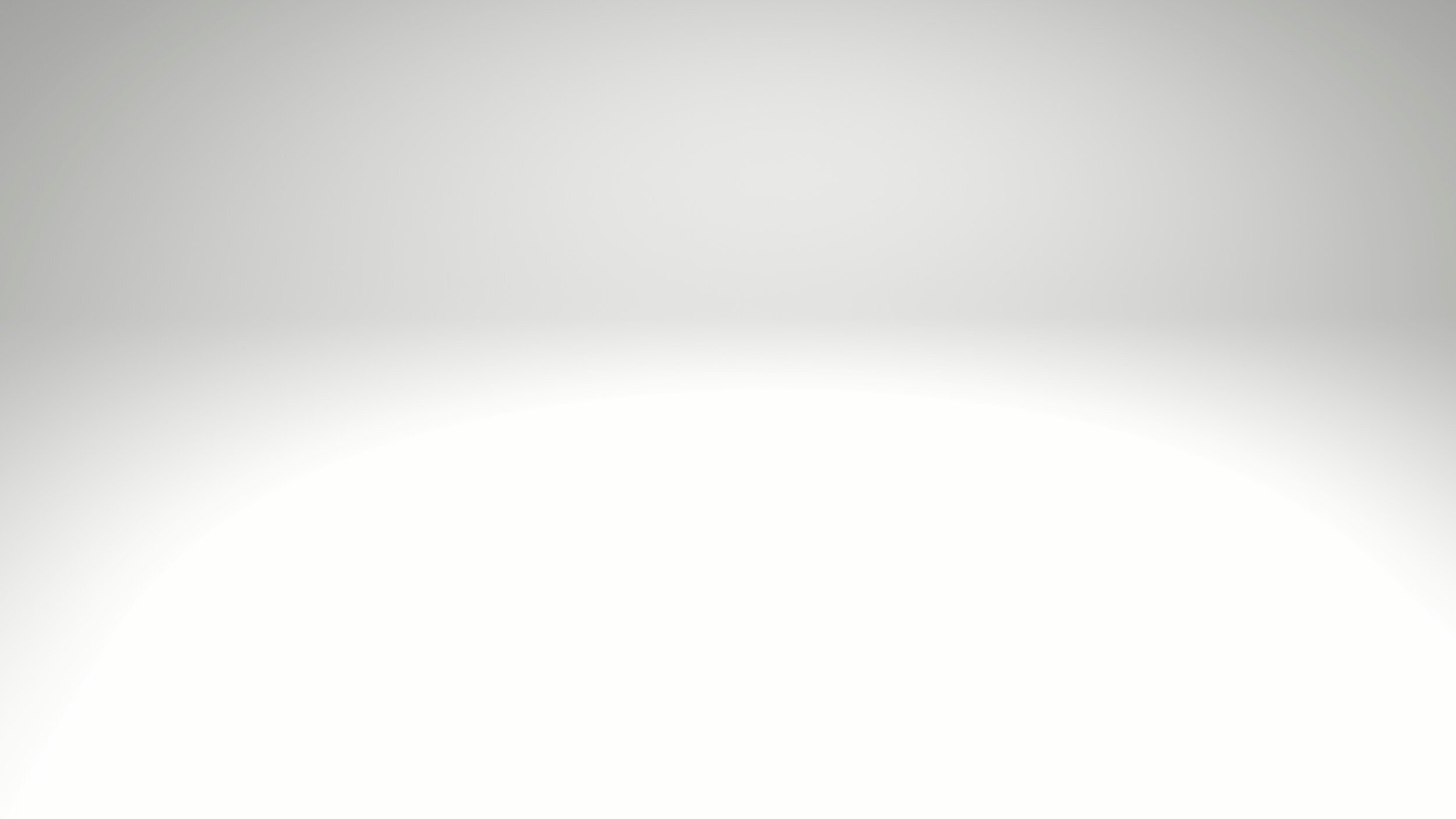
19305
Weld Blending Cell
ACT-19305 is a precision weld blending machine that utilizes a 6-axis robotic articulated arm, blade scanner, and a finishing process that yields consistent and accurate airfoil shape, blade height, and chord width of tip weld repaired blades. ACT-19305 eliminates hand grinding of weld tip repaired blades, increases productivity, minimizes scrap rate, and produces consistent blade geometry at a very low cost of consumables. The tip welds are ground to within 0.002” (0.05mm) from airfoil without cutting into the substrate material.
6-axes articulated robotic arm with controller
Grinding stations
Part surface and weld scanner
Indexer for part loading
Part tooling
Base and Enclosure
Dust collection ducts
Options
Automatic gripper change
Squealer groove grinding
Final inspection and measurement with data collection
Offline programming software
For more information, contact us at sales@actrobots.com
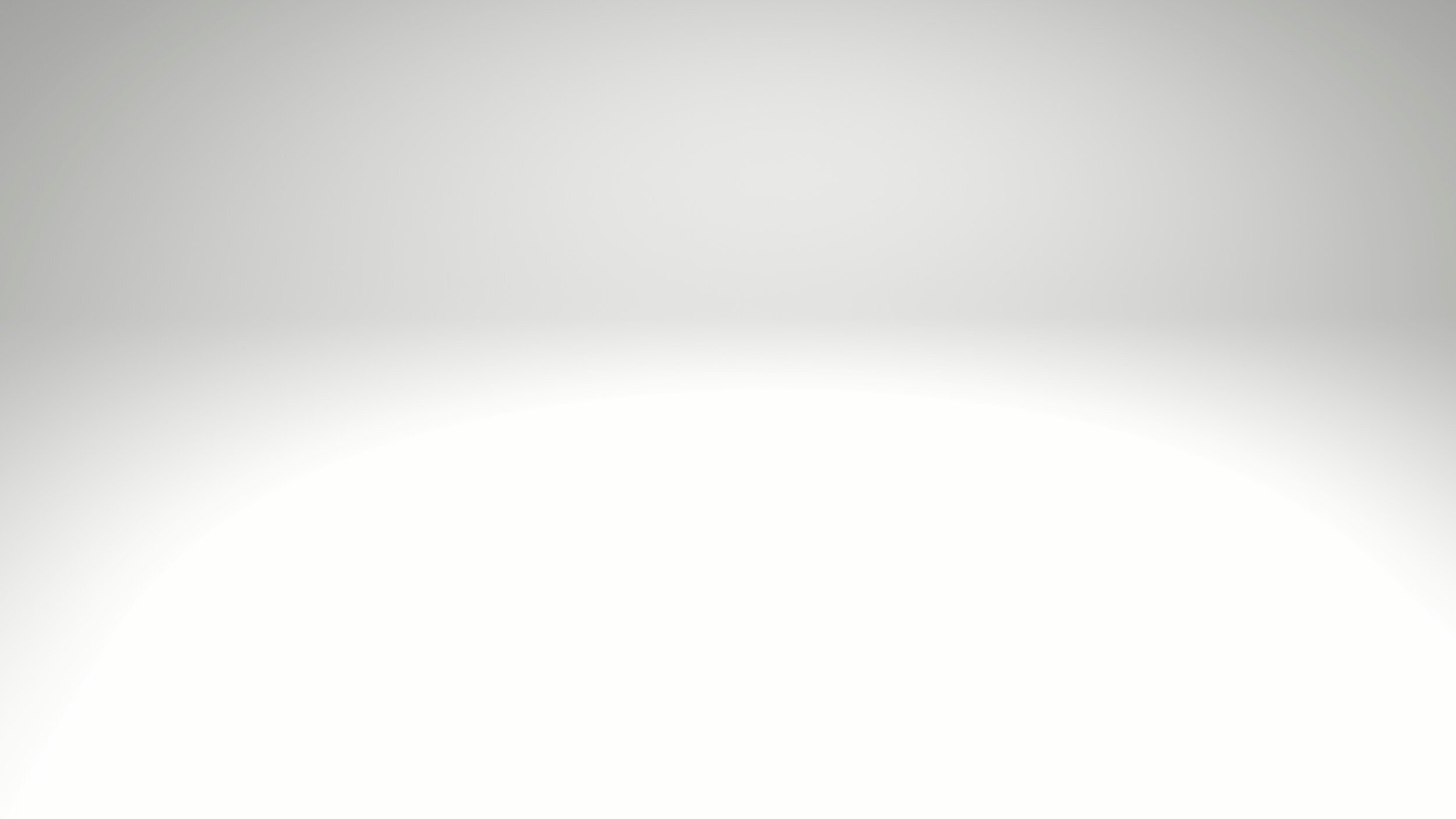
18996
Blade Polishing Cell
ACT-18996 is a robotic cell for polishing blades and other smaller parts. It had a robotic arm, part load drawer(s), vision scanner, polishing area with 3 wheel spindles, down-draft dust collection, and tool/gripper magazine.
Robotic arm (20 kg payload)
Automatic tool changer adapter EOA
Tool/gripper magazine with gripper and wheel arbors docking nest
Three auto collet 1/2HP servo wheel spindles
Two part load/unload drawers
Options
Vision scanner
Re-grip station for parts reorienting
Wet or dry dust collector
For more information, contact us at sales@actrobots.com
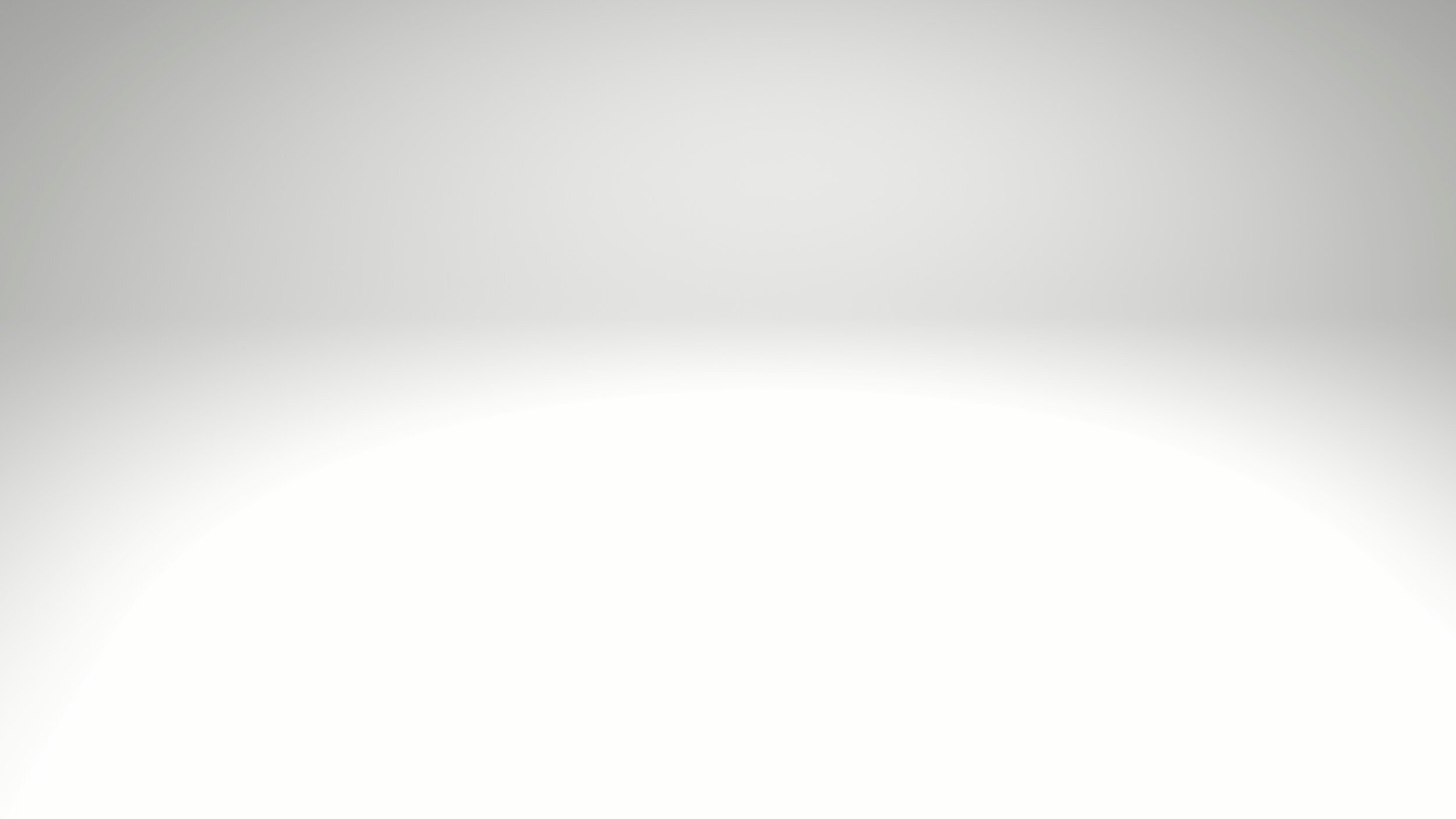
18996-0001
Blade Polishing Cell
ACT-18996-0001 is a robotic cell for polishing blades and other smaller parts. It had a robotic arm, part load drawer(s), vision scanner, two separate polishing areas with 3 wheel spindles and down-draft dust collection, and finally tool/gripper magazine.
Two separate polishing areas to process parts of different materials which cannot mix such as steel and aluminum or titanium
Robotic arm (20 kg payload)
Automatic tool changer adapter EOA
Tool/gripper magazine with gripper and wheel arbors docking nest
Three auto collet 1/2HP servo wheel spindles
Two part load/unload drawers
Options
Vision scanner
Re-grip station for parts reorienting
Wet or dry dust collector
For more information, contact us at sales@actrobots.com
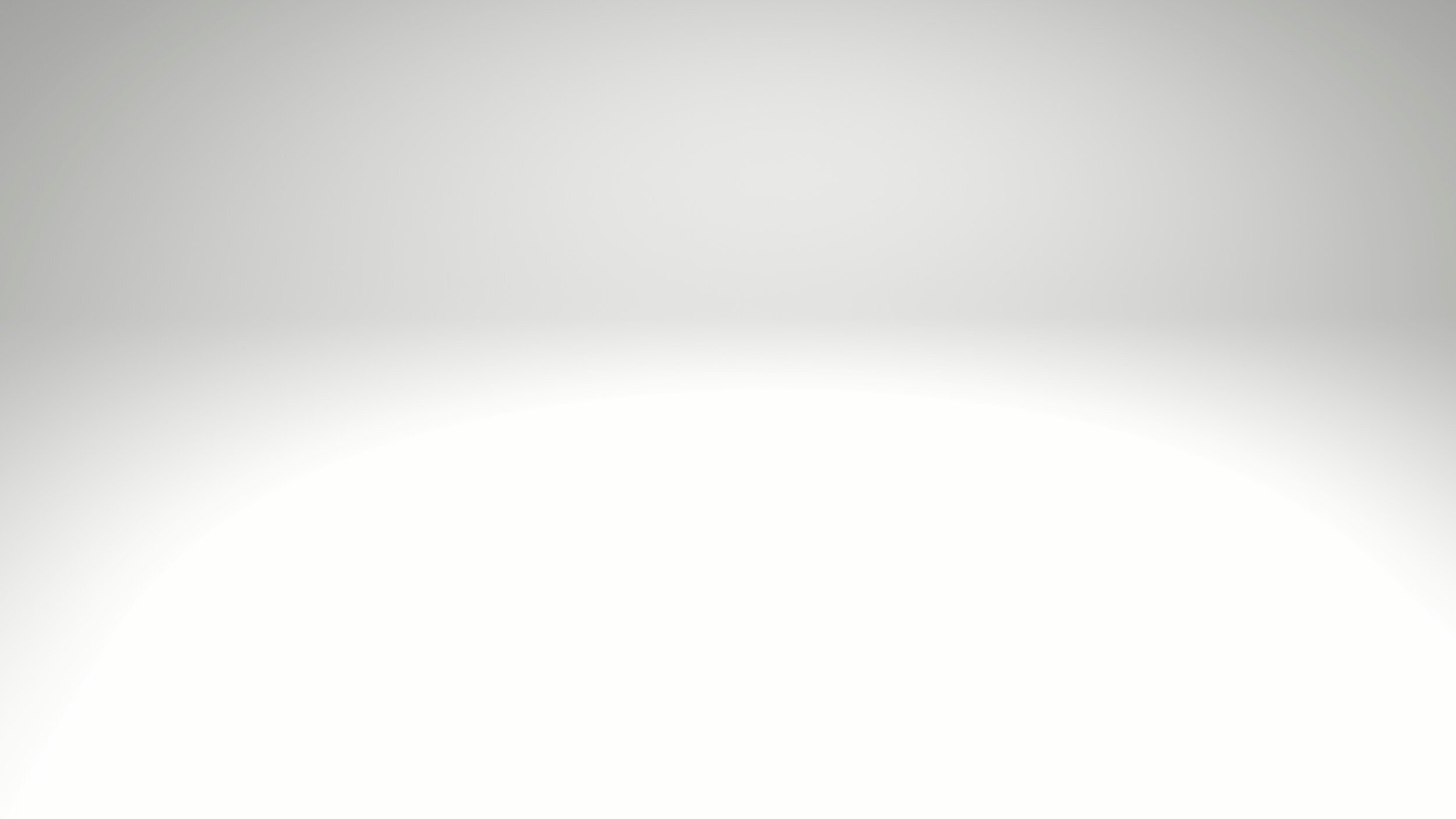
07226
Cell with 4 Belts Over/Under and Cart
ACT-07226 is a polishing or grinding cell for parts such as door handles or faucet fixtures, requiring a 3-5 step abrasive process.
Robotic arm (50-80 kg payload)
Gripper for long barrels with rotating lathe
Four 5HP belt heads in an over/under configuration
Dual wheel 5HP head
4-sided vertical part load magazine (tombstone) on 90 deg indexer
Human Machine Interface
Enclosure and base
For more information, contact us at sales@actrobots.com
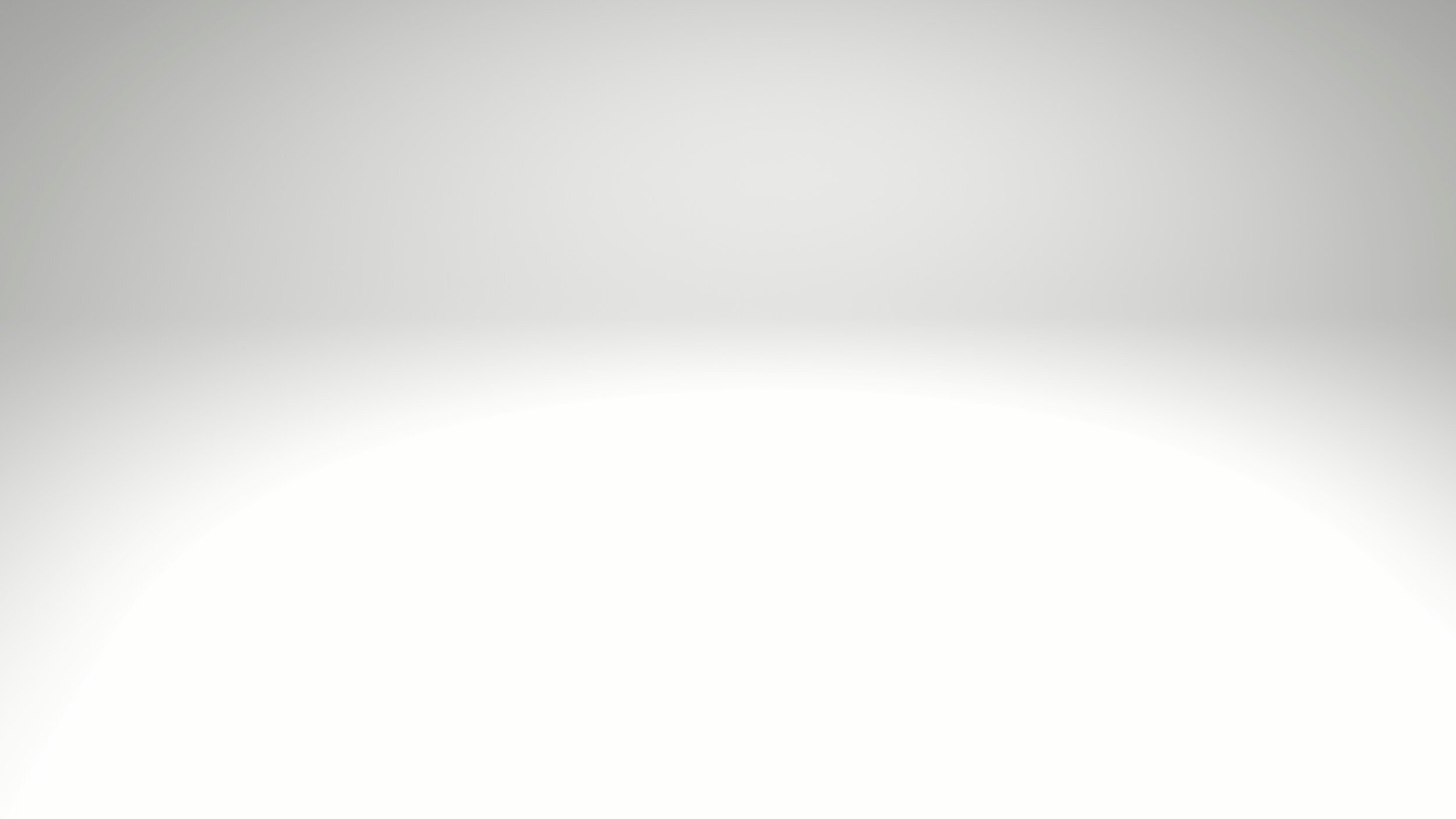
18301
Polishing and Burnishing Cell for Plastic Parts
ACT-18301 is a polishing/burnishing cell for light plastic parts with precise flat surface polishing. This cell utilizes robotic arm with pneumatic floating pusher to hold and press parts against static sandpaper on precision plate fore very accurate flatness polishing of plastic parts surfaces. Parts are dragged across the abrasive in a programmed pattern while floating tool pushes down with programmable force. The float mechanism keeps part flat against the grinding plate thus eliminating errors from robot and gripping. Abrasion sandpaper feeds automatically when used to present fresh section for next batch of polishing.
Robot arm (12-24 kg payload)
End of arm tool with gripper for part handling and programmable floating pusher for polishing
Sandpaper roller feeder with precise polishing plate
Interlocked part load area
Part and tool detection sensor
Enclosure and base
For more information, contact us at sales@actrobots.com
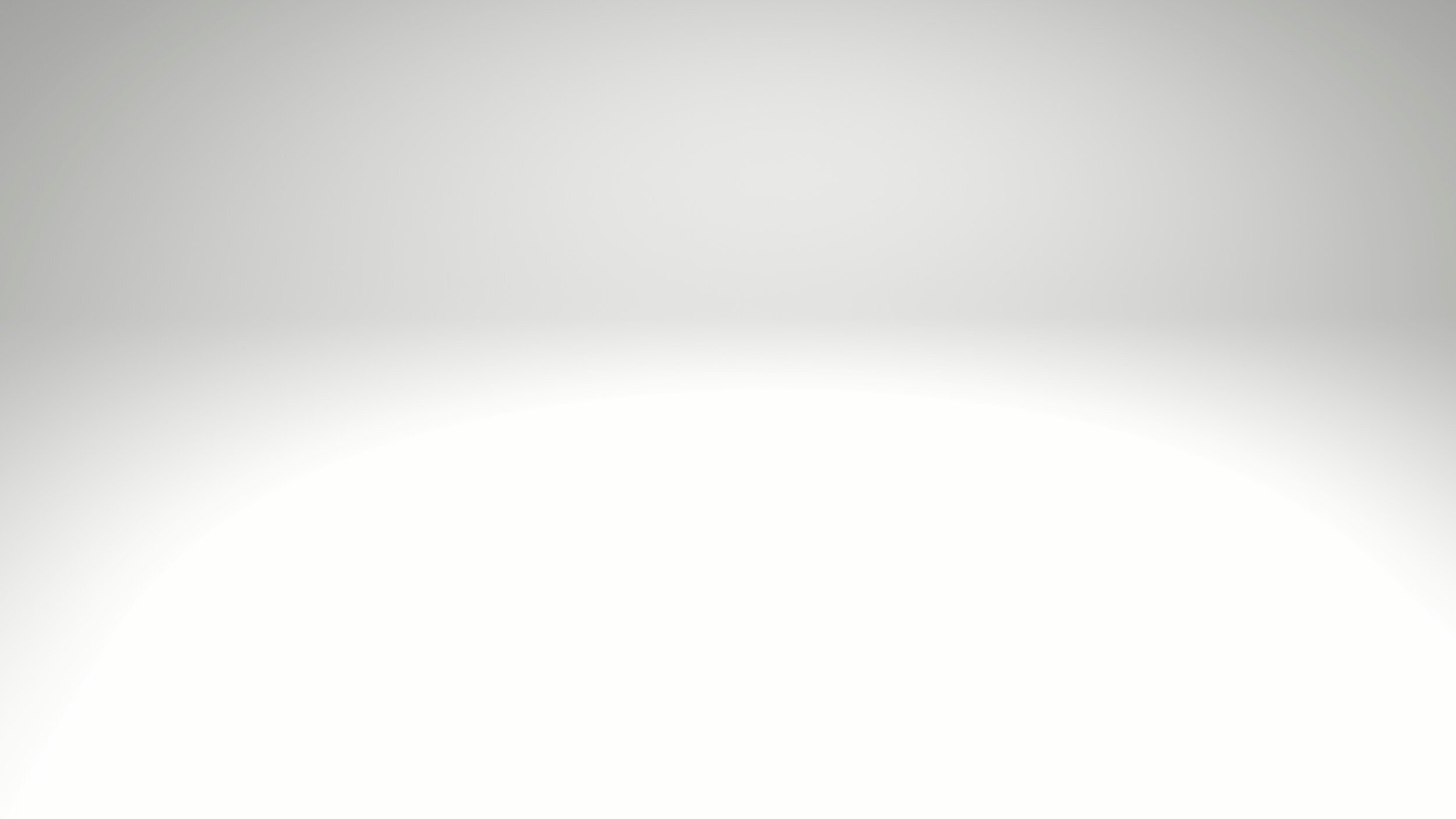
17997-0000.122217
Polishing or Deburring Cell
ACT-17997-0000.122217 is a polishing or deburring robotic cell with a base floor integrated down-draft style dust collector. This cell is portable and self contained with 6-10 kg robotic arm, part load drawer, rotary indexer tool magazine, high speed debur spindle, small wheel spindle, two 5HP wheel heads, small belt head, and dust collector in the floor.
Robot Arm (6-10 kg) w/ auto tool changer EOA
High speed deburring spindle with 360 degree compliance
Two servo or air driven spindles for small wheels up to 6" OD
Two wheel heads, both 5HP, with auto collet spindles for quick or automatic wheel change
Small belt tool with radial compliance for belts up to 1/2" W x 18" L
Part load drawer
Rotary indexer tool magazine with up to 16 tool docking positions
Re-grip station with 2-jaw gripper and 180 deg rotary index
Down-draft dust collector integrated in machine base
Enclosure and base
Human Machine Interface (HMI)